Fascinating glass production
Turning sand into a unique product
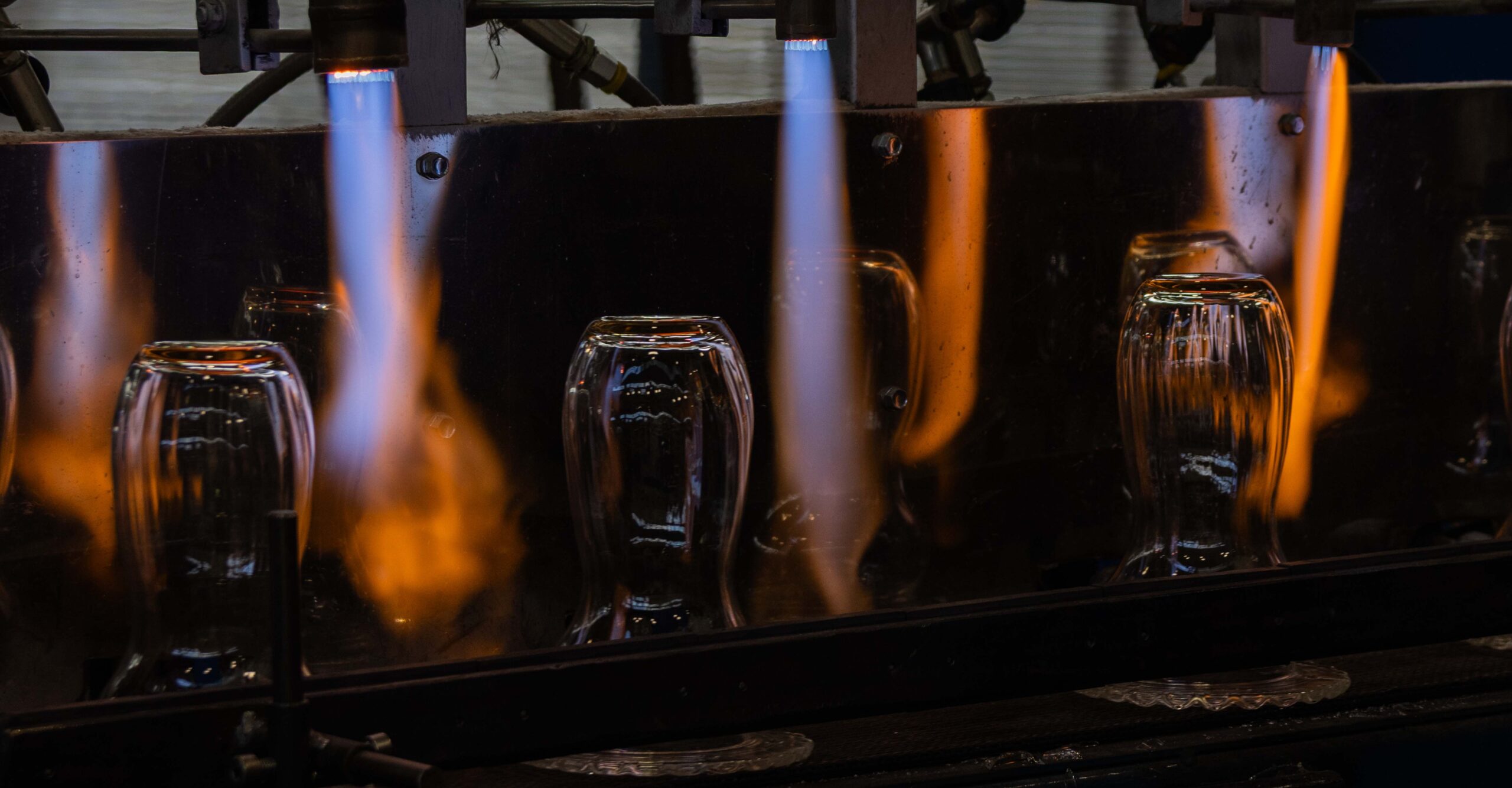
Glass is one of the oldest and most widely used materials known to mankind. In fact, it has been in production for almost 5,500 years. It has been used not only in architecture and design, but also for the production of drinking and utility glass, which we use today and every day. But to better understand exactly how glass is made and what crystal glass is actually made of, let’s go through the entire process, including the key stages.
What is glass anyway?
Glass is an amorphous (i.e. non-crystalline) material that is formed by melting glass-forming raw materials and then cooling them at such a rate that the material does not form a crystalline lattice with a regular structure. Interestingly, in terms of physical properties, the finished glass is still a liquid, but its viscosity is so high that we cannot see it with the naked eye. Only with the passage of hundreds of years would it be more or less possible to observe changes in shape or thickness. In glassmaking terminology, the molten mass is called glass; the solidified material is already glass, which can be further refined.
Glassmaking is a complex and fascinating process that involves a wide range of raw materials and technologies. From the preparation of glass raw materials to the melting and shaping process to the final finishing, each step is essential to the production of quality glass that finds applications in our everyday lives. As an amorphous material, glass provides both aesthetic and functional benefits, making it an important element of modern industry.
High-quality crystal glass also has excellent optical properties, which add to its attractiveness and give it a high gloss and maximum transparency. These include perfect light transmission, increased refractive index and dispersion.
What is glass made of? Glass sand plays a major role
Glass comes in different forms, which are directly influenced by the chemical composition of each type of glass. What is glass made of? The basic ingredient for glass production is silica, also known as glass sand (SiO2). However, the actual melting of the sand requires a high amount of energy, and it should be noted that the resulting glass is far from meeting normal requirements. In this case, other raw materials must be used to produce the glass, but we will come to that later.
Glass made only from quartz sand is referred to as quartz glass and its main application is in the field of refractories. In order to achieve the properties of glass that we know from everyday life, it is necessary to add additional ingredients to the sand, including chemistry, which include fluxes, stabilisers, clarifiers, hardeners and dyes.
Ideal raw materials and the right chemistry are the key to success
Glassmaking is, in a word, alchemy. To get the best possible properties, the right chemistry is also needed. First of all, there are fluxes such as potassium carbonate (K2CO3) or sodium carbonate (Na2CO3), which, depending on the composition, significantly reduce the melting temperature of the glass sand from 2000 to 1200-1500 °C. These additives also affect the time for which the glass remains mouldable. Glass can practically be divided into ‘short’ and ‘long’ – potassium carbonate produces ‘short’ glass, which is ideal for mass production, while sodium carbonate produces ‘long’ glass, which is particularly suitable for hand forming and precision modelling.
Traditionally, long glass was produced mainly in Venice, giving rise to the term Venetian glass. Short glass, which is harder and better suited to decorative work such as engraving and cutting, is found in the countries north of the Alps.
If fluxes are added during the production of the glass, the thermal properties of the glass itself are improved, but at the same time its chemical resistance is reduced to such an extent that the glass becomes soluble in water, resulting in water glass. This problem can be avoided by adding stabilisers to the mixture, the purpose of which is to significantly increase the chemical resistance of the glass. Examples of stabilisers include calcium carbonate (CaCO3) or lead oxide (PbO), which improve the optical properties of the glass, including the refractive index of light.
Other raw materials used in the production of glass include ceramics, which help dissolve gases in the glass. Hardeners are used if we want to achieve opalescent, i.e. opaque glass. Coloring agents, usually in the form of precious metals, produce specific colors in the glass due to their oxidation in the enamel. For example, gold gives a pink colour, while cobalt gives a dark blue colour.
In terms of glass terminology, we distinguish not only glass sand, but also glass strain, which is formed by combining bulk mixtures – silica together with fluxes, stabilizers and dyes. However, if glass cullet is added to the glass cullet, the mixture becomes glass ware. The prepared mixture is then gradually loaded into the furnace by the louver stacker, where it is spread evenly over the surface of the already fused glass. Interestingly, the Crystalex brand returns shards to the glassmaking process to the maximum possible extent – in the range of up to 95%, thanks to which almost no unused glass is wasted. Almost all glass waste is recycled. The entire glass production process is as environmentally friendly as possible.
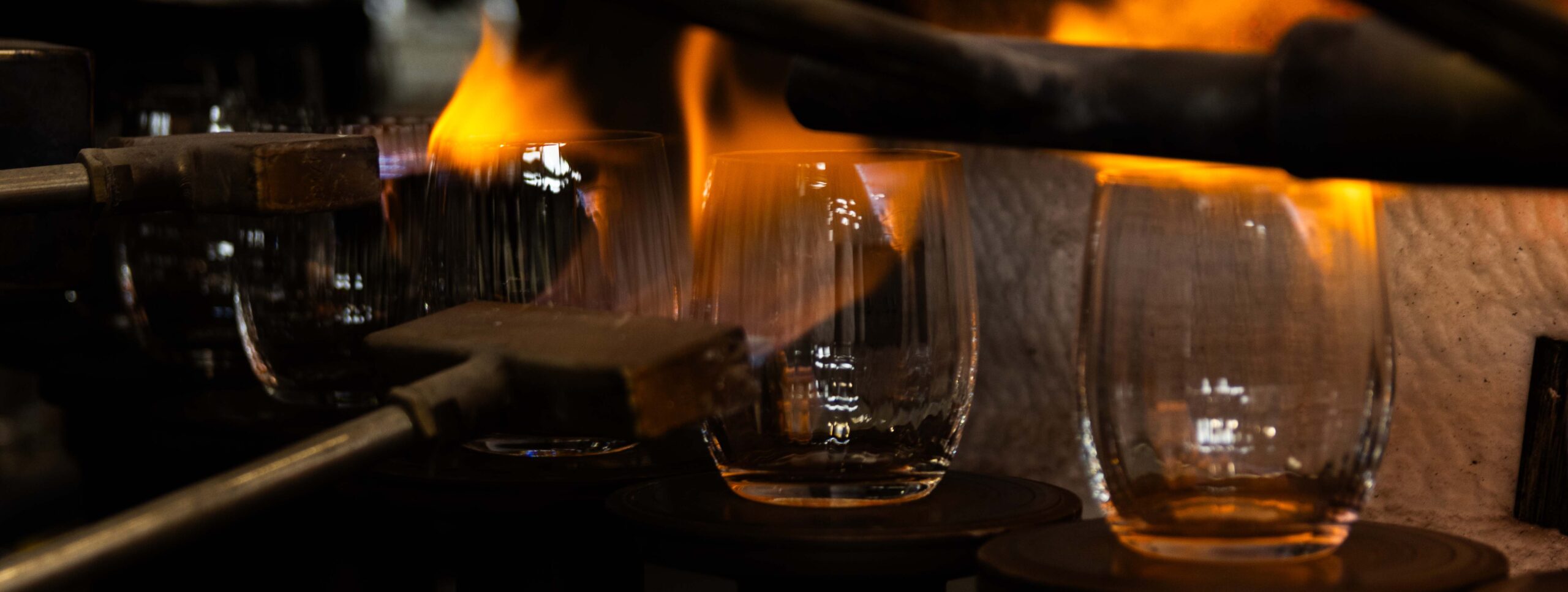
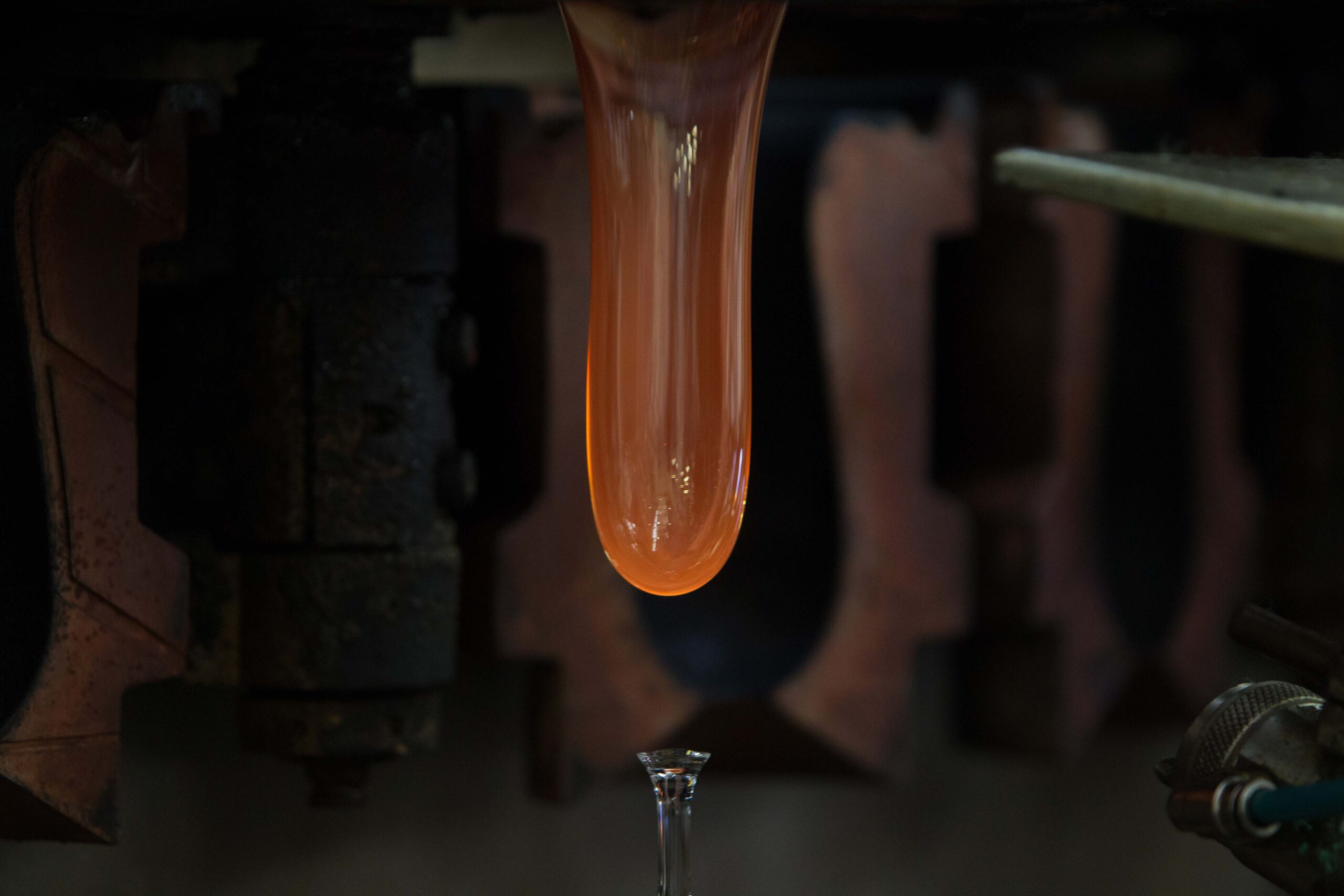
How is glass made? The correct procedure is important
Now that we know what glass is made of, it’s the perfect time to move on to the next step, the actual production of the glass. The glass furnace, which can be a pan or bath furnace with electric or gas heating, plays a crucial role in this respect. How do they differ?
Pan furnaces
For pan furnaces where glass is melted and shaped periodically, it is important to plan the time for both melting and shaping. The glass is melted overnight and shaped during the day. They are mainly used for small-scale production or manual removal. They are melted in pans located inside the furnace and their capacity is in the order of units and lower hundreds of kilograms. Gas heating is the most common.
Bath furnaces
In contrast, bath furnaces, which operate continuous melting, produce glass continuously. Compared to ladle furnaces, they are generally larger and have a capacity of several tens of tonnes. The melting process in a bath furnace has no breaks, so it operates continuously and the melting process itself takes place along the entire length of the furnace – sand is poured at one end and glass flows out of the other. Bath furnaces heat with both gas and electricity using electrodes in the glass. The glass itself does not conduct electricity, but the molten glass does.
Our brand relies on both gas and electricity to produce glass. The latter, however, is significantly more dominant than gas. The melting of glass in our large-scale furnaces is carried out exclusively using electricity, which is also used by the compressors and production lines. Gas also plays an important role in our production. It ensures the operation of the cooling furnaces and the glass forming technology.
The melting process begins in a special room called the strain room, where the raw materials are stored and then mixed in a precise ratio. It is essential to follow the correct procedure when making glass, because only then will the glassmakers obtain a product of high quality and optimal properties. The melting process itself takes place in four stages:
- Melting – during melting, chemical reactions occur between individual components and their gradual melting into a hot mass – enamel.
- Homogenization – takes care of thorough mixing of the enamel to avoid inconsistencies, defects or any other imperfections in the enamel.
- Polishing – removes miniature air bubbles from the enamel, which were formed during the melting of the deposit. Polishing is done either chemically or mechanically using a compressor that produces large artificial bubbles that collect the smaller ones from the surface. These would not be allowed to escape from the mass by the surface tension and density of the glass.
- Screening – because the cleaned glass is very thin, the temperature of the enamel must drop to the working temperature, which is the temperature at which the glass can be optimally shaped.
However, before the enamel leaves the furnace area to be transformed into the final product, its temperature must drop to the working temperature. This is the temperature at which the glass has the optimum viscosity, and therefore formability, for a particular production technology.
Each glassworks has its own unique recipe, which it guards closely, and it is no different in the case of Crystalex, which has the Bohemia Sparkle™ trademark for its glassware and also holds the Bohemia Crystal™ trademark, which guarantees the highest quality materials and production processes.
Manual and automated glass forming has its charm
Glass production is divided into manual and automated. Hand-blown glass is the result of a traditional process that involves many techniques most often passed down from generation to generation. Hand-blown glass has a rich tradition, with the first glass blowing pipe having been invented by the Phoenicians 2,000 years ago. The glass whistle plays a major role in shaping the glass, as does the glassmaker, who uses it to scoop up the molten glass and blow it into the final product. Hand-blown glass has a long tradition, especially in the Nový Bor region, and is most often used for the production of smaller pieces. Wooden moulds made of beech wood are mainly used for handmade production.
If we look into the history of the Crystalex brand, there was originally a glassworks where glassmakers hand-blowed glass. But as demand grew, manual production was no longer able to meet the demands of so many customers, so in 1972, as part of an innovation, the first automated line for mass production was put into operation for the first time. In fact, one automated line is capable of producing around 1200-1500 pieces per hour, whereas manual production can produce several dozen pieces in the same amount of time (and assuming the same product). Today, therefore, a total of seven machines are operating in the production plant, the vast majority of them for machine-blown calico. If they are all in operation at the same time, we can produce up to 210,000 pieces of glass per day. Thanks to this, we are able to supply not only the domestic but also the foreign market.
On the other hand, machine glass forming includes modern technologies such as blowing, pressing, press-blowing and centrifugal processes. In particular, the key element in automated glass production is the feeder, which determines the amount of enamel required for each shape. It batches and cuts a drop of the required size and weight. The drop then falls into the punch, which pre-presses it to the required diameter and then transfers it to the blow mould (metal moulds are used for automated production). The still hot glass flows by gravity into the mould, which is closed – after the mould is closed, the product is blown and shaped on the basis of the mould used. After blowing, it is important to cool the product controllably in a cooling oven, which removes internal stresses and thus saves the glass from breaking. Also important in automated production is the lance, simply put, the extra piece of glass that must be cut off before final finishing with a laser, which in glassmaking parlance means a swelling. After the beading, the top edge of the glass is sealed with a flame to prevent it from being sharp, while at the same time hardening it. However, as there is nothing like physical inspection by sight, the final inspection is twofold – electronic (involving a box with optical systems and cameras) and manual (carried out by workers).